Beyond the Box: A Deep Dive into HMI Enclosure Customization and Design for Optimal Performance
- Share
- Issue Time
- Jul 19,2025
Summary
Unlock the full potential of your industrial equipment with our expert guide on HMI enclosure customization. Learn how to select the right materials, design for harsh environments, and implement features that enhance usability, ensuring your HMI systems are protected, ergonomic, and perfectly aligned with your operational needs.
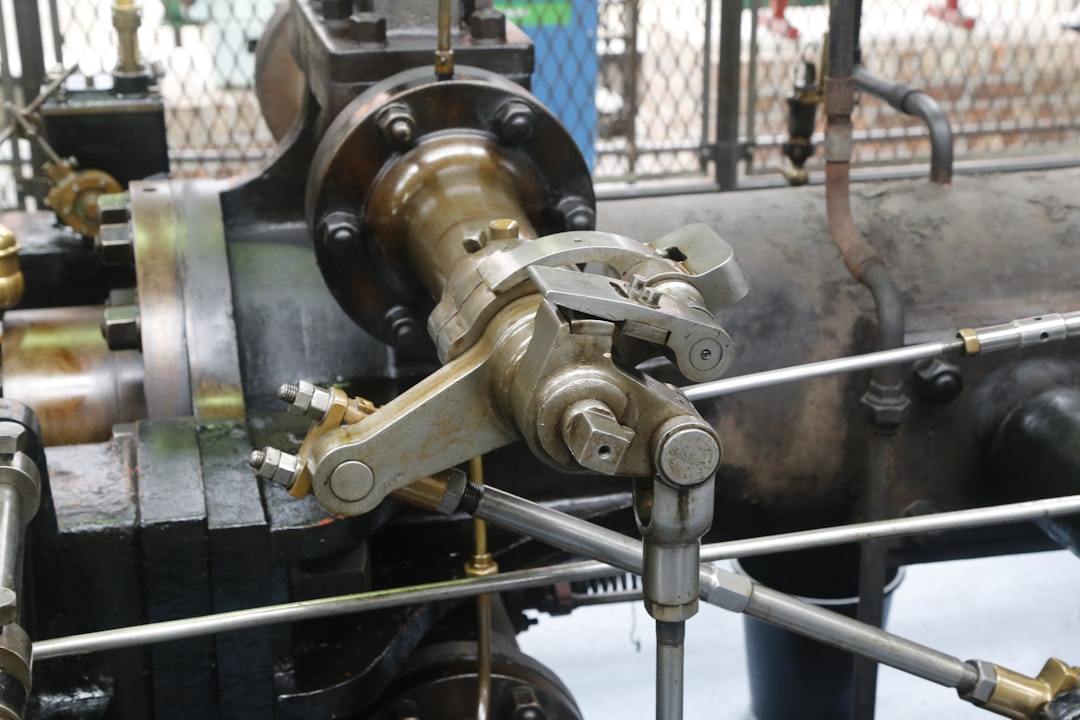
Why Standard HMI Enclosures Don't Always Make the Cut
In the world of industrial automation, the Human-Machine Interface (HMI) is the critical link between operator and machine. While a standard enclosure provides a basic level of protection, it often falls short of meeting the unique demands of a specific application or environment. Off-the-shelf solutions may not have the correct dimensions, material composition, or a layout that is ergonomic for the operator. This is where customization becomes not just a luxury, but a necessity for ensuring safety, efficiency, and longevity of the sensitive electronic components within. A truly effective HMI system relies on an enclosure designed with its specific operational context in mind.
Starting with the Right Foundation: Material Selection
The first and most crucial step in designing a custom HMI enclosure is selecting the appropriate material. The choice depends heavily on the operational environment, including exposure to chemicals, moisture, and physical impact.
- Steel: Robust and durable, steel enclosures are a reliable choice for many industrial applications. They provide excellent protection against physical impact. Carbon steel is a common option, often powder-coated for added resistance.
- Stainless Steel: For industries like food and beverage or pharmaceuticals, stainless steel is the gold standard. Its superior corrosion resistance makes it ideal for environments with harsh cleaning agents and high-hygiene requirements.
- Aluminum: Lightweight yet strong, aluminum offers a great balance of durability and ease of handling. It naturally resists corrosion by forming a protective oxide layer and is excellent at dissipating heat.
- Polycarbonate: These plastic enclosures are lightweight and offer good protection against impact and certain chemicals. They are often used for smaller, handheld, or wall-mounted units.
The Core of Customization: Tailoring the Physical Design
Custom fabrication allows for an enclosure that fits your HMI components like a glove. Modern manufacturing techniques make it easier and more cost-effective than ever to create bespoke designs even in low volumes. A key aspect of this is the ability to specify precise cutouts.
Precision Cutouts and Sizing
One of the most significant advantages of custom design is the ability to specify the exact size of the enclosure and the placement of cutouts for screens, buttons, switches, and cable glands. CNC machining ensures that these apertures are cut with precision, providing a perfect fit for your components and maintaining the integrity of the enclosure's seal. This eliminates the need for on-site modifications that can compromise the enclosure's protective ratings.
Access and Mounting Solutions
How operators and maintenance staff interact with the HMI is a critical design consideration. Custom enclosures can feature a variety of access options, including hinged rear doors, removable front plates, and secure locking mechanisms. Furthermore, they can be designed for specific mounting requirements, such as:
- Suspension/Support Arm Systems: These allow the HMI to be positioned ergonomically for the operator and moved out of the way when not needed.
- Pedestal Mounting: Ideal for freestanding applications.
- Wall Mounting: A space-saving option for fixed locations.
- VESA Compatibility: Adhering to this standard ensures easy integration with a wide range of mounting hardware.
Protection from the Elements: Understanding NEMA and IP Ratings
To ensure your HMI is adequately protected, it's crucial to understand environmental protection ratings. The two most common standards are NEMA (National Electrical Manufacturers Association) in North America and IP (Ingress Protection) internationally. These ratings define the enclosure's ability to resist solids (like dust) and liquids (like water). Choosing an enclosure with the correct rating is vital for reliability.
NEMA Rating | IP Equivalent (Approximate) | Protection Against | Common Applications |
---|---|---|---|
NEMA 1 | IP20 | Incidental contact, falling dirt | Indoor use in non-hazardous locations. |
NEMA 3R | IP24 | Rain, sleet, snow, external ice | Outdoor wiring and junction boxes. |
NEMA 4 | IP66 | Windblown dust, rain, splashing water, hose-directed water | Indoor/outdoor use with occasional washdowns. |
NEMA 4X | IP66 | Same as NEMA 4, plus corrosion | Harsh environments with corrosive agents, such as food processing. |
NEMA 12 | IP54/55 | Dripping and light splashing of non-corrosive liquids, circulating dust | Indoor industrial and automation control. |
NEMA 6P | IP67 | Entry of water during prolonged submersion | Applications with a risk of temporary submersion. |
Enhancing Usability Through Ergonomic Design
A well-designed HMI enclosure goes beyond mere protection; it enhances the operator's ability to do their job safely and comfortably. Ergonomics is a key consideration, especially for interfaces that are used frequently. Mounting HMIs on adjustable support arms allows operators to position them at a comfortable height and angle, reducing physical strain.
Adding the Finishing Touches: Accessories and Aesthetics
Customization extends to the finer details that improve functionality and branding. Adding accessories like keyboard trays, handles, or protective windows for screens can significantly improve the user experience. Aesthetically, enclosures no longer need to be plain grey boxes. They can be finished in custom colors and feature printed logos or graphics, reinforcing brand identity and reflecting the sophistication of the machinery within.
The Future of HMI Enclosures: Smart and Integrated
The trend in HMI enclosure design is moving towards smarter, more integrated solutions. Enclosures are becoming more than just protective boxes; they are an integral part of the control system. With the rise of Industry 4.0, we see more flush-mounted glass panels for a sleek, modern look and enclosures designed with thermal management in mind to dissipate heat from increasingly powerful internal components.
Selecting the Right Manufacturing Partner
To bring a custom HMI enclosure design to life, it is crucial to partner with a manufacturer that has extensive fabrication expertise. Look for a provider who can handle the entire process in-house, from initial design and CNC machining to finishing and assembly of accessories. This ensures a streamlined process, consistent quality, and a final product that is perfectly tailored to your requirements.
Source URLs:
- ARCA-IPW - HMI Covers - Fibox Enclosures
- HMI Enclosures - TZR Sheet Metal
- HMI Enclosures - KDM Fabrication
- Custom HMI Screen Enclosures | Custom Display Panel Enclosure - CamdenBoss
- HMI Enclosures | AutomationDirect
- multiPANEL - The premium design HMI enclosure - ROLEC
- Concept HMI Enclosure Type 4 | nVent HOFFMAN
- HMI Enclosures - Quador
- HMI Enclosures - TROPAC - Industrial Electrical Solutions
- Effortless Customization: How Modern HMI Enclosures Meet Rising Expectations
- Hoffman HMI Enclosures: Various Sizes 10 - RSP Supply
- Modern HMI/Display Panel Enclosures | ROLEC USA
- Made to measure HMI and display panel enclosures
- Control Enclosures - ROSE Systemtechnik GmbH
- Tips for Selecting and Positioning Industrial HMIs and Control Panels | Machine Design
- Environmental Protection of HMI Components A Technical Help Guide - Mouser Electronics
- PRODUCT BROCHURE - HMI Enclosures
- IP-HMI406025 HMI Enclosure
- HMI Enclosures - Airline Hydraulics
- NEMA ratings for enclosures - Applied Mechanical Technology
- NEMA Enclosure Ratings and IP Equivalents
- NEMA Ratings for Enclosures